Zwiększenie mocy systemu chłodzenia
Zwiększenie mocy systemu chłodzenia
Klient
Nasz klient to znany producent specjalizujący się w wytwarzaniu części metodą formowania wtryskowego dla przemysłu opakowaniowego. Firma stanęła przed poważnym wyzwaniem związanym z niewystarczającą mocą systemu chłodzenia, co skutkowało zbyt wysoką temperaturą chłodzenia wtryskarek.
Problem
Głównym problemem klienta była niezdolność istniejącego systemu chłodzenia do odpowiedniego wychłodzenia zarówno form jak i hydrauliki maszyn, co powodowało zakłócenia operacyjne oraz niską efektywność produkcji.
Możliwości
Po przeprowadzeniu kompleksowej inwentaryzacji i analizy zakładu produkcyjnego klienta zidentyfikowaliśmy następujące kluczowe punkty:
- Firma wykorzystywała system chłodzenia składający się z jednego sprężarkowego agregatu chłodniczego o mocy chłodniczej około 380 kW i dodatkowego agregatu chłodniczego o mocy 300-400 kW (wynajęty), z których oba były odpowiedzialne za chłodzenie zarówno form, jak i obwodów hydraulicznych za pomocą wody lodowej o temperaturze około 10°C.
- Obliczona moc chłodnicza wymagana do chłodzenia form wynosiła 300 kW.
- Obliczona moc chłodnicza wymagana dla obwodu hydraulicznego wynosiła 620 kW.
Rozwiązanie
Po dokładnej ocenie systemu klienta zaleciliśmy następujące rozwiązanie w celu wyeliminowania nieefektywności systemu chłodzenia:
- Oddzielenie obwodu chłodzenia form i obwodu chłodzenia hydrauliki, ponieważ miały one różne wymagania temperaturowe.
- Wdrożenie dodatkowego obiegu chłodzenia o temperaturze 30°C specjalnie dla układu hydraulicznego, wykorzystującego free cooling bez potrzeby stosowania chillera sprężarkowego.
Korzyści
Wdrażając drugi obieg chłodzenia, klient zyskał:
- Wyraźne rozdzielenie obiegów w oparciu o różne kryteria temperaturowe, zapewniające precyzyjną kontrolę temperatur w obiegu chłodzenia form i hydrauliki.
- Zwiększenie temperatury chłodzenia obiegu hydraulicznego do 30°C, pozwoliło na zmniejszenie zużycie energii i kosztów operacyjnych całej produkcji,
- Odciążenie obiegu chłodzenia form, ustabilizowanie temperatury i wyeliminowanie potrzeby stosowania drugiego agregatu chłodniczego (rezygnacja z wynajętego chillera),
- Zmniejszenie całkowitego zużycia energii dzięki wykorzystaniu free coolingu do chłodzenia układu hydraulicznego, zwłaszcza że przy produkcji opakowań metodą wtrysku większość ciepła jest generowana przez układ hydrauliczny,
- Zwiększone bezpieczeństwo systemu dzięki separacji obwodów, co zmniejsza ryzyko awarii całego systemu.
- Efektywność energetyczna całej produkcji.
Trochę faktów
- Szczytowy pobór energii elektrycznej przez chiller sprężarkowy o mocy chłodniczej 620 kW (temperatura wody lodowej 30/20’C, temperatura otoczenia 25°C): 157 kWh.
- Szczytowy pobór energii elektrycznej przez free cooler o mocy 620 kW (temperatura wody lodowej 35/30’C, temperatura otoczenia 25°C): 45 kWh.
- Pobór energii elektrycznej chillera sprężarkowego przy temperaturze otoczenia -20°C i pełnym obciążeniu: 65 kWh.
- Pobór energii elektrycznej free coolera przy temperaturze otoczenia -20°C i pełnym obciążeniu: do 3 kWh.
- Chiller sprężarkowy – 7 stopni regulacji.
- Free cooler – 12 stopni regulacji – dużo większa możliwość odciążania, niż w przypadku chillera sprężarkowego.
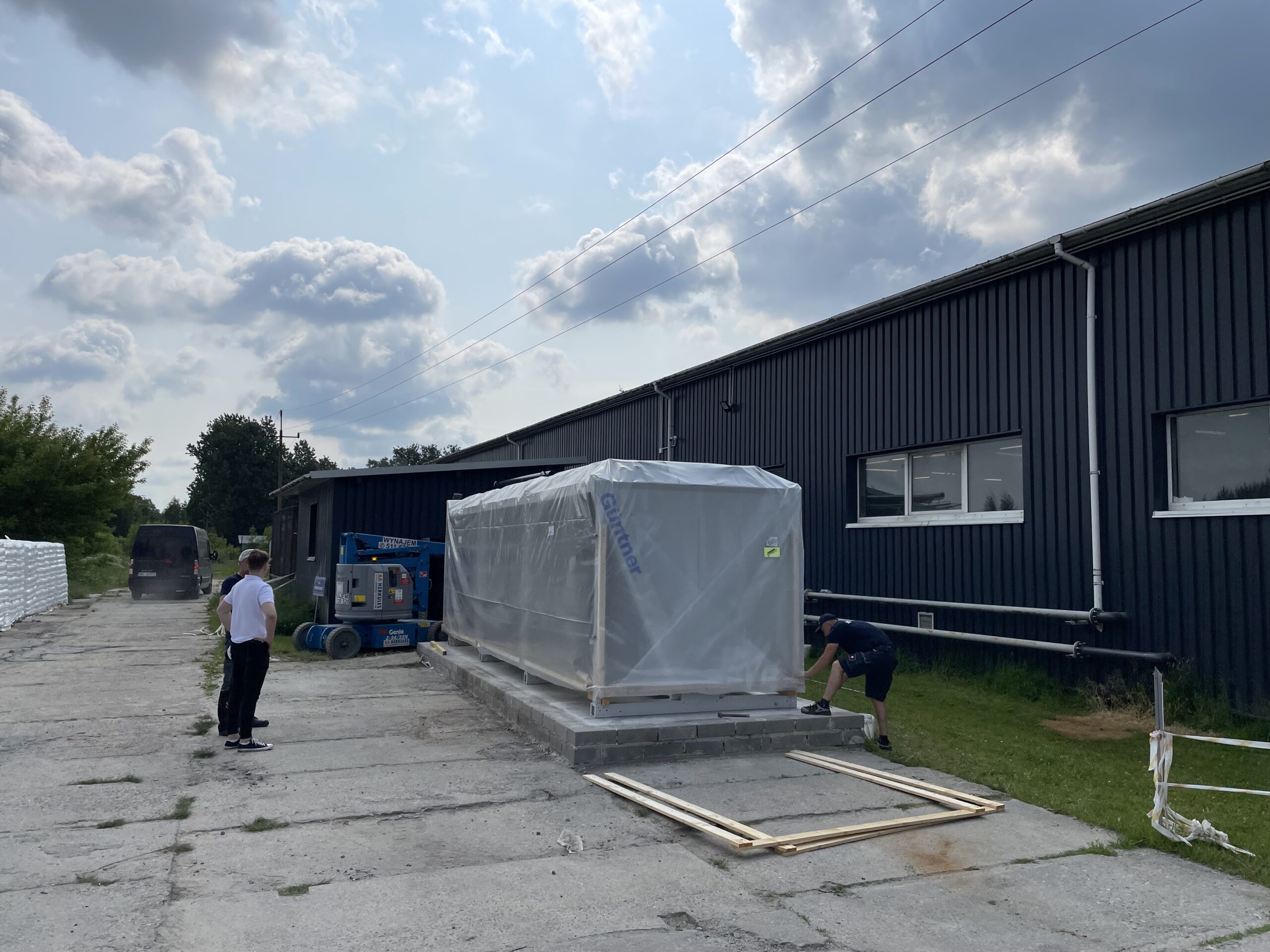